EMS Desulphurisation
Desulphurisation
Flue gas desulfurization is the process of removing Sulphur compounds from the exhaust emissions of fossil-fueled power stations. This is done through the addition of absorbents, which can remove up to 95% of the Sulphur dioxide from the flue gas. Flue is the emitted material produced when fossil fuels such as coal, oil, natural gas, or wood are burned for heat or power. The currently widely applied methods for desulfurization are wet desulfurization, semi-dry desulfurization, and dry desulfurization.
- Wet desulfurization: Desulfurization with
- limestone/lime-gypsum
- Desulfurization with ammonia
- Semi-dry desulfurization
- Dry desulfurization
Desulphurisation System
The currently widely applied methods for desulfurization are wet desulfurization, semi-dry desulfurization, and dry desulfurization. The following typical proven process methods are introduced
1. Wet desulfurization:
Desulfurization with limestone/lime-gypsum
Process description:
Fume is boostered into the desulfurization tower from the bottom and rises in the tower to have contact with sprayed lime milk mist, which removes the SO2, SO3, HF, and HCI, etc. Lime milk is produced and sent to lime milk tank to mix with lime gypsum. A circulating pump sends the slurry to the spraying layer where lime milk mist is sprayed.
After removal of SO2 in the spraying layer, the fume goes to mist separator.
SO2 and suspended lime mist particles reacts and produces CaSO. Air forced by an oxidizing fan enters the oxidizing air lance arranged in the slurry tank so that the CaSO can be oxidized into CaSO4. During the reaction, the lime-gypsum can be crystallized from the saturated solution. Lime-gypsum slurry is then pumped to vacuum dewatering unit to remove water.
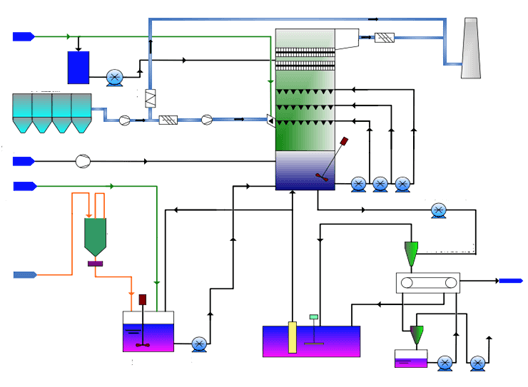
Process advantages/disadvantages
Advantages
- Teliable technology
- Low investment
- Affordable raw material
Disadvantages
- High water consumption
- Difficulties in CaSO4 treatment
- High steam content in emission
Process description
Fume is boostered into flue to enter the absorbing tower for thickening, absorption, and scrubbing respectively to remove the SO2. After that, mechanical mist separator can remove the moisture and dust. Finally, the treated gas is discharged into atmosphere via stack.
Ammonia solution in absorbing section is oxidized and then flows to thickening section. After thickening, it goes to filter to remove the dust. Clean liquids from filter goes to evaporator where the sulphate-ammoniate solution is heated by steam up to saturation. Crystallized sulphate-ammoniate is sent to cyclone. The overflow from the cyclone goes to absorbing tower; its underflow goes to centrifuge; liquids from centrifuge returns to absorbing tower. Moist ammoniate-sulphate goes to dryer; dried ammoniate-sulphate goes to packing unit.
Process flow diagram
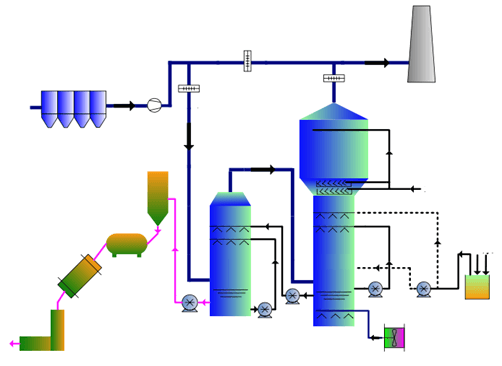
Process advantages/disadvantages:
Advantages:
- Reliable technology
- Low operation cost
- Products can be sold
Disadvantages:
- High water consumption
- Emission may condense into water falling on to the ground
- High steam content
Rotating mist spraying
Process description:
Fume is boostered to the SDA tower and reacts with sprayed lime milk mist to remove the SO2. During the reaction, some CaSO3 is converted into CaSO4.
Quick lime fines are charged into a tank to produce lime slur (15-25%). Lime slur is vibrated before flowing into the lime slur tank which pumps the slur to the tower top according to the process requirement. From the tower top, the slur atomizer converts the slur into 50um mist which absorbs SO2 in the fume. Products from desulfurization are also small particles, which allow quick reaction and quick drying.
Particles contained in the gas flow are caught by bag filters; treated gas is discharged to the atmosphere. Collected dust under the deduster is taken away periodically. Large size particles (sand or dissolvable lime stone from limestone fines) sink into the tower bottom.
Process flow diagram:
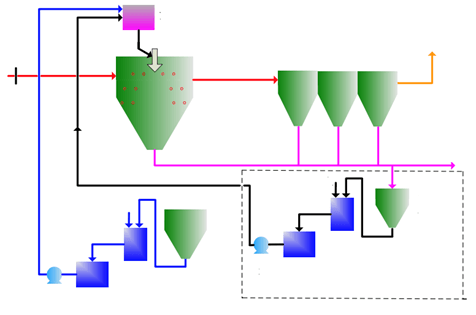
Process Advantages/Disadvantages
Advantages
- Reliable technology
- Low water consumption
- No steam in emission
Disadvantages
- Difficult to handle the products
- High investment
Desulfurization with active coke
Process description
Fume is boostered into absorbing tower to react with active coke which absorbs SO2 and NOx. Treated fume is discharged into atmosphere via stacks.
Active cokes that have absorbed SO2, NOx, dioxin, heavy metals, and dust are screened first; the oversize cokes are conveyed to stripper; the undersize cokes and dust are sent to dust bin for consumption as fuel.
Gas containing SO2 stripped from reactive cokes is sent by fans to H2SO4 production line which produces H2SO4 of 98%.
Process flow diagram
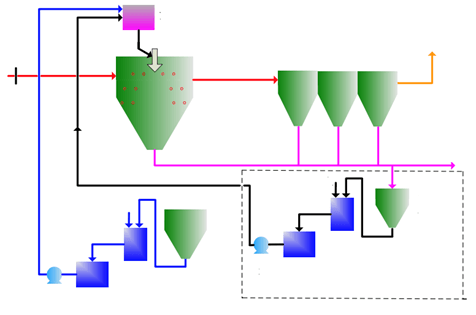
Process advantages/disadvantages
Advantages
- Reliable technology
- Very low water consumption (only for cooling of fan and pump)
- No steam in emission
- SCR and desulfurization simultaneously
- Recyclable products
Disadvantages
- High investment on construction and operation
- Large land area requirement
One Stop Solution for All Your Epc Requirements
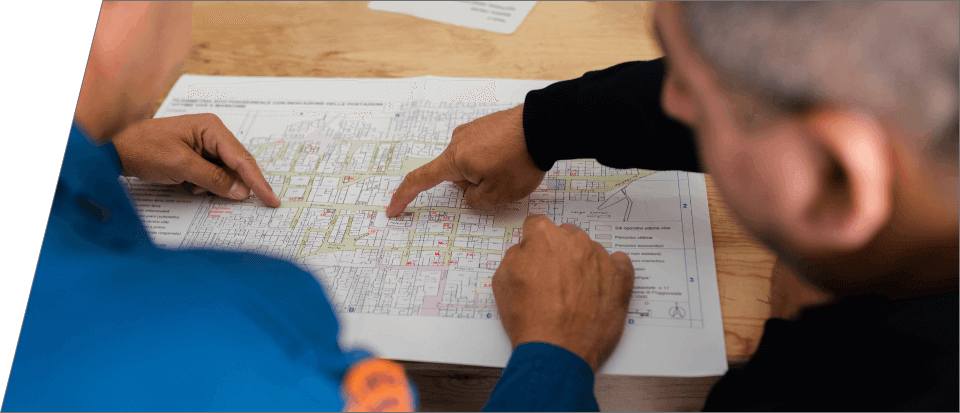
Our Clients



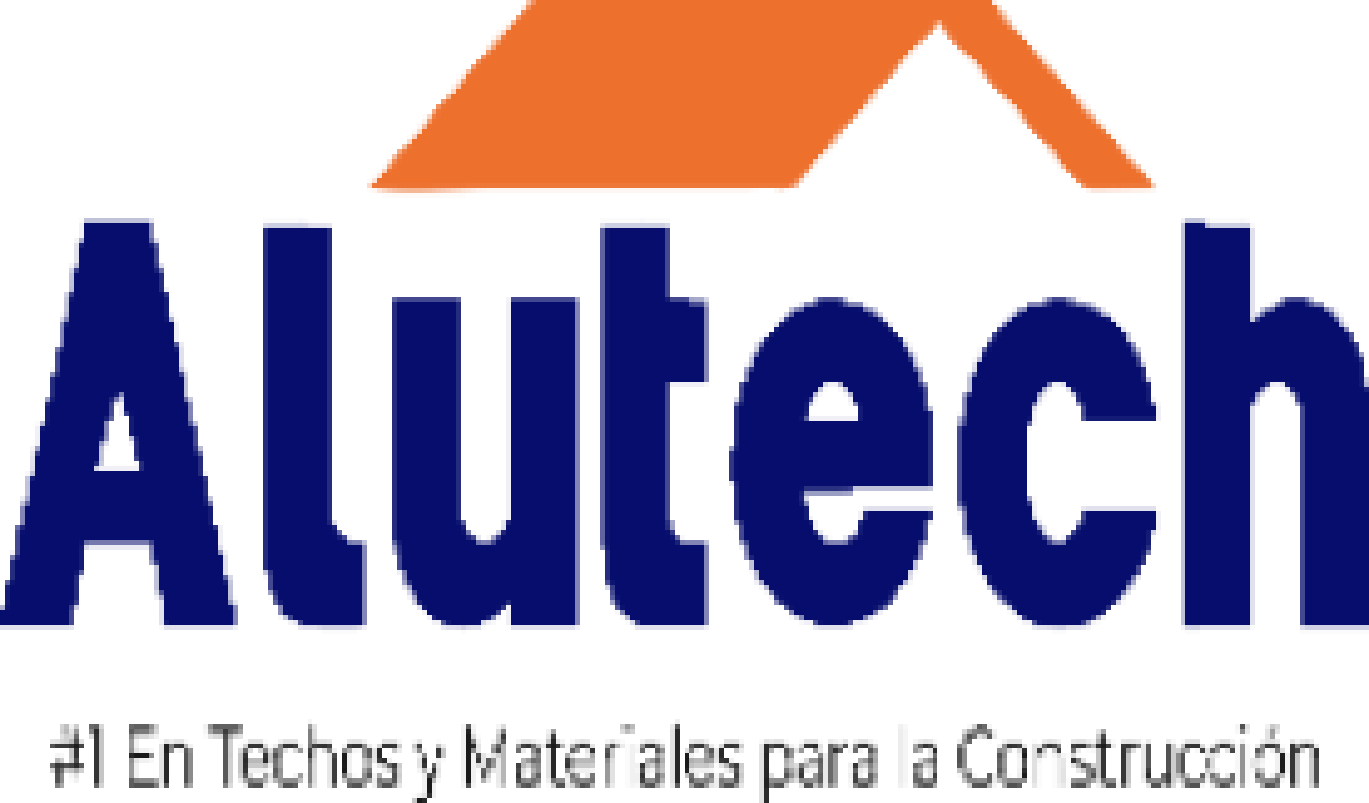